Main Structure and Components (Inward Valve Type)
- Tie Rods: Securely connect the front head, cylinder, and back head.
- Back Head: Houses oil ports, gas valve, and is filled with N₂ gas.
- Valve: Controls piston movement inside the valve housing.
- Cylinder: Contains the hydraulic circuit; the core of the breaker.
- Piston: Converts kinetic energy into impact energy to break rock.
- Front Head: Supports breaker structure; contains upper bushing to absorb shocks.
- Tool: Heat-treated tool (e.g., moil, wedge, flat) used to break rock (optional types).
- Accumulator: Stabilizes hydraulic pressure and absorbs pulsation (charged with N₂ only).
General Safety Precautions
Read and understand all manuals and warning labels before operation.
Only trained personnel should operate or service the breaker.
Follow all applicable laws and site regulations.
Never operate the breaker with anyone in the danger zone.
Keep controls neutral before engine start.
Shut off the engine before inspection, maintenance, or repair.
Do not exceed 80°C (175°F) hydraulic oil temperature.
Only use original BEIYI breaker tools and components.
Never operate under the influence of alcohol, drugs, or impairing medication.
Always remove breaker during machine transport.
Keep the manual with the breaker at all times.
Preparation for Installation
GENERAL VIEW OF BREAKER INSTALLED:
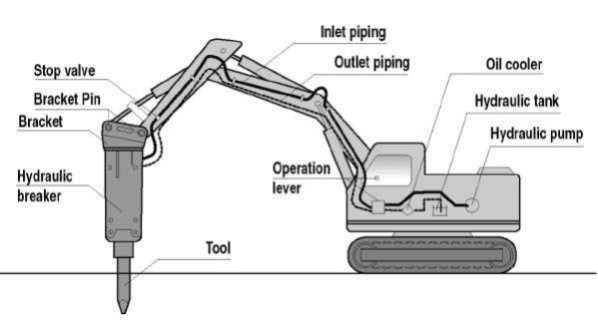
HYDRAULIC PIPE LINES FOR EXCLUSIVE USE
Operation of the hydraulic breaker requires installation of hydraulic pipe lines for exclusive use of the hydraulic breaker. As hydraulic pipe lines vary depending on base machines, our service engineer must first check hydraulic pressure, oil capacity, pressure loss and other conditions of the base machine before installing hydraulic pipe lines. Use only genuine parts in case of replacement because hydraulic pipe lines (hoses, pipes and fittings) are made of materials carefully selected in consideration of durability.
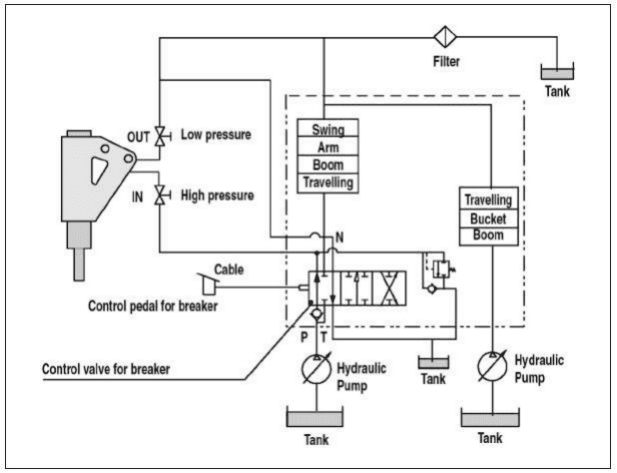
Operation Guidelines
A. PROPER POSITION OF THE TOOL
Proper position must be applied for an effective use of breaking force. When position is incorrect, blowing energy of the piston is too weak to break rocks.
Instead, blowing force applies shocks to the breaker body, breaker, arm, and boom of the base machine, thereby resulting in damage to those parts.
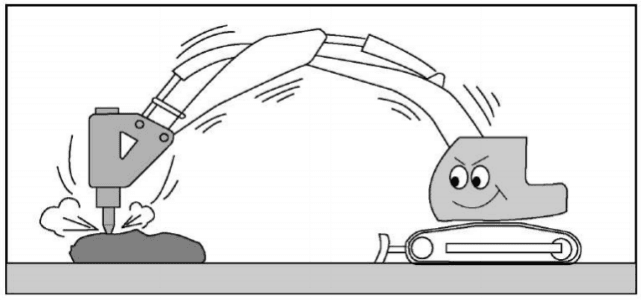
On the contrary, when position is excessive enough to break rocks with front of the base machine raised, the machine may suddenly tilt forward the moment rocks are broken then the breaker body or the end of bracket may violently hit against rocks and result in damage.
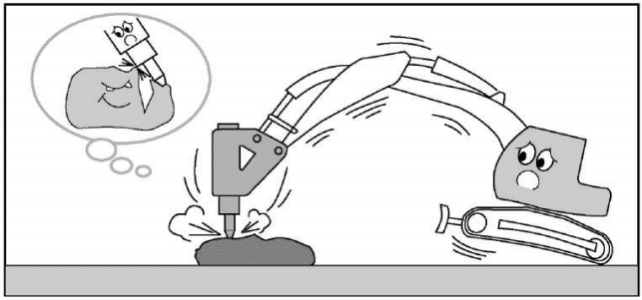
It is undesirable to carry out hammering under the below condition, because vibrations during hammering may be transmitted to tracks of the base machine.
During hammering, however, proper position must be always applied to the breaker. Special care must be taken not to hammer under abnormal conditions.
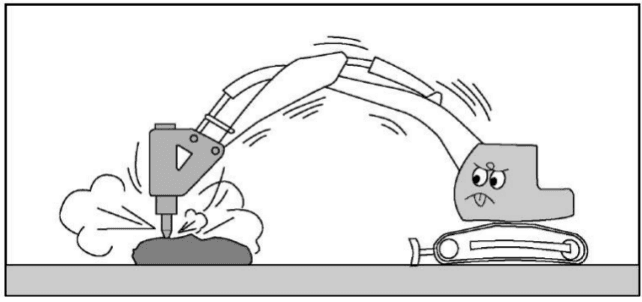
B. Tool Alignment
Apply same direction of boom force in line with the tool and place the tool in the rock with hammering
surface as vertical as possible. If hammering surface is oblique, the tool may slip during hammering.
This causes the tool to seize and to be broken and piston to be damaged. When breaking, fully stabilize the tool first and then select the point of a rock on which hammering can be performed in a stable condition.
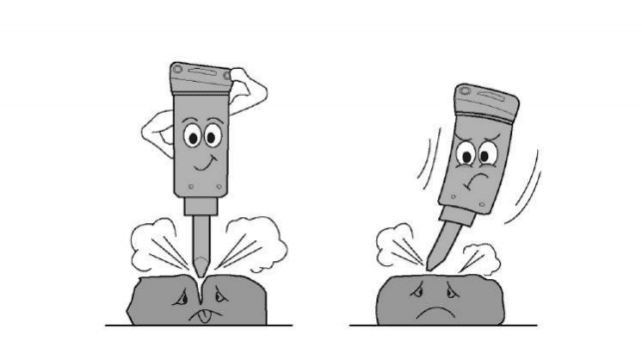
C. Operating Tips
- Stop operation as soon as hose vibrates excessively.
Excessive vibration of high and low-pressure hoses of breaker calls for an instant disassembly and repair. Contact the nearest service station appointed by Dsbreak . For caution’s sake, check oil leakage at the back head.
- The operator is required to pay attention to the following points during operation.
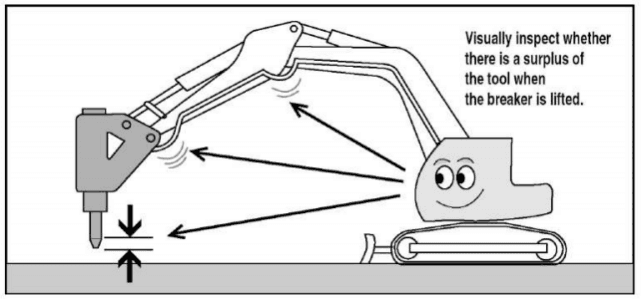
- Avoid all blank hammering
As soon as the rocks are broken, stop hammering. Continuous blank hammering will not only damage front head and loosen and break bolts, but also adversely affect base machine.
Blank hammering occurs when proper position of the tool is not applied to the breaker or the tool is used as a lever. (Hammering sound changes during blank hammering)
- Do not move rocks
Avoid moving rocks with side of the bracket, because it is the major factor to break bolts installed on the bracket, tool and damage boom and arm.
- Do not use tool as a lever
When breaking rocks by using tool as a lever, bolts and tools may be broken, too.
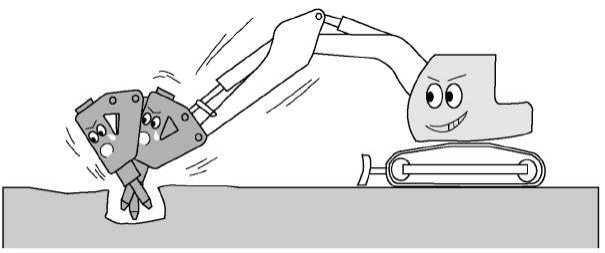
- Do not continue to hammer for more than one minute.
When rocks are not broken after more than one minute of hammering at the same point, change the place to be hammered. Extended hammering at the same place causes the tool to wear out excessively.
- On a hard and large rock, start breaking at start breaking from the edge.
Even a hard and big rock can be easily broken when hammering begins at a crack or an edge.
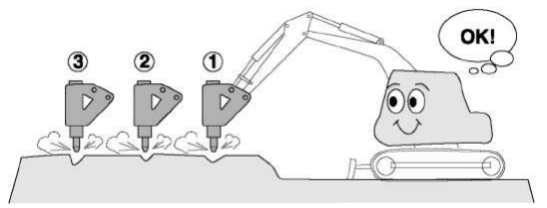
- Operate breaker at proper engine speed.
Break rocks at the specified engine speed.
Raising engine speed more than necessary does not strengthen hammering force but increase oil temperature to the detriment of pistons and valves.
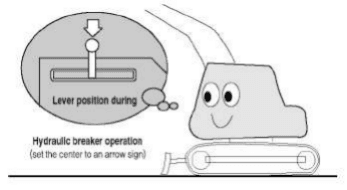
- Do not operate the breaker in water and mud.
When rocks are not broken after more than one minute, Do not operate breaker when all components
except tool are immersed in water and mud. Piston and similar components may gather rust and become a
damaged breaker at an early stage.
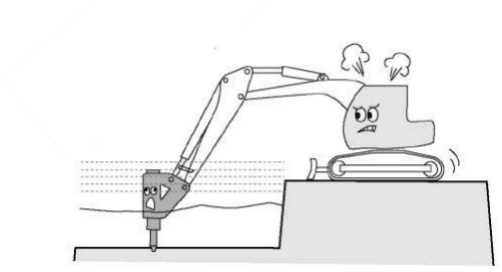
- Do not allow the breaker to fall to break a rock.
Falling down the breaker will apply excessive force to the breaker or the base machine, causing damage to many parts of the breaker and the base machine.
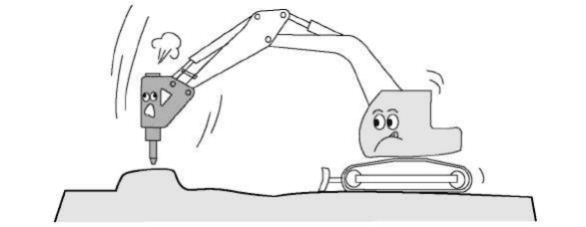
- Do not hammer with base machine cylinders moved to stroke end.
Hammering with each base machine cylinder moved to stroke end (a condition that the cylinder is fully extended or retracted) will do considerable damage to the cylinder and each part of the base machine.

- Do not lift things with the breaker.
Lifting materials by hanging wire in the bracket or tool not only causes damage to the breaker but is also very dangerous when operating.
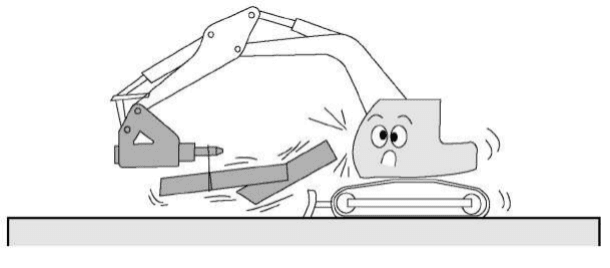
- Warm up base machine engine prior to operation.
Especially in winter, the base machine engine should be warmed up for five to ten minutes at 30°C~40°C (86°F~105°F) before breaker operation. Follow the instruction book for base machine to warm up the engine.
- Do not touch tool for breaker working
While the breaker is working, high temperatures of the tool will be generated.
l When operating the breaker, you must use ear and body protection. You must use ear and breathing protection when the breaker is operating.
- Accumulator-type danger
Pay attention to the pressurized container! Do not open without reading the manual or consulting with the authorized service personnel!
- Greasing
With breaker mounted on carrier, apply down pressure on tool, and fill cavity with recommended grease through the grease nipple.
Personal Protection & Maintenance
Always wear hearing, eye, and respiratory protection when operating.
The accumulator is a pressurized container: Never open it without authorization.
Grease the tool regularly: With the breaker pressed down, apply grease via the nipple.
Wear eye protection when removing the stop pin with a hammer and punch.